High-pressure switches have extremely high-proof pressure limits to function in pressure systems with high pounds per square inch. They can also be helpful in pressure systems operating within normal ranges. Still, they might occasionally experience pressure surges or spikes pushing the systems’ normal psig (pounds per square inch, gauge) values past the limit. High-pressure switches will continue to function properly and enable continuous pressure control, whereas conventional pressure switches would malfunction in such circumstances. Read More…
Tecmark is a designer and manufacturer of remotely actuated controls used by OEMs worldwide. We offer an extensive line of high pressure switches, and our customer service representatives will help you find the perfect model for your application. Whether you are looking for an in-house solution, or an industry need, we continue to develop technological advancements.
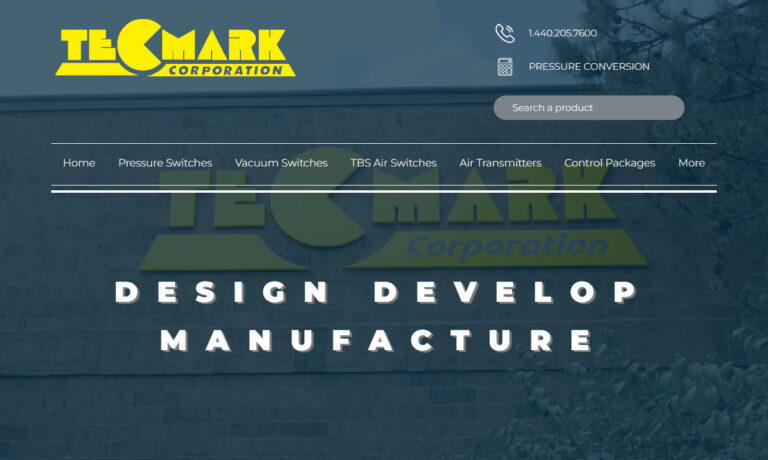
SOR pressure switches have earned a long-time reputation for their high quality, rugged construction and reliable performance under the most demanding applications. We offer explosion proof, hermetically sealed, and weatherproof switches. We design our pressure switches with high performance in mind, crafting custom, durable pressure switches with the approval of multiple agencies. Our products...
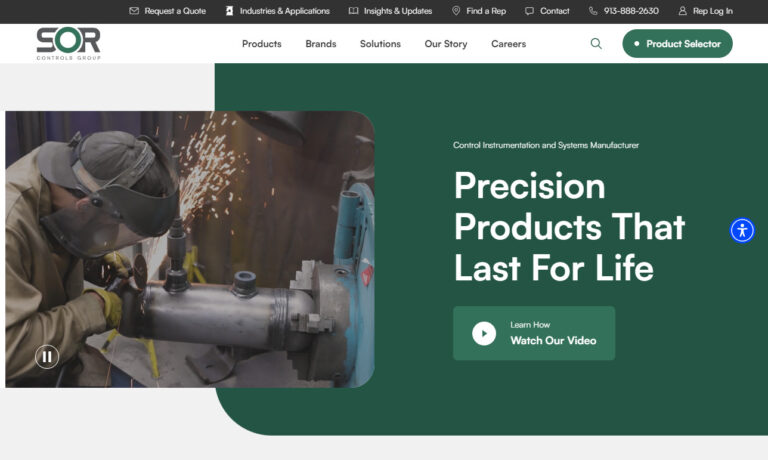
For over 35 years, MPL has specialized in unique miniature pressure switch solutions to the world’s leading manufacturers. MPL pressure sensors and switches can be found in the most demanding environments from automotive to health care where long-life, reliable solutions are required. Visit our website for details.
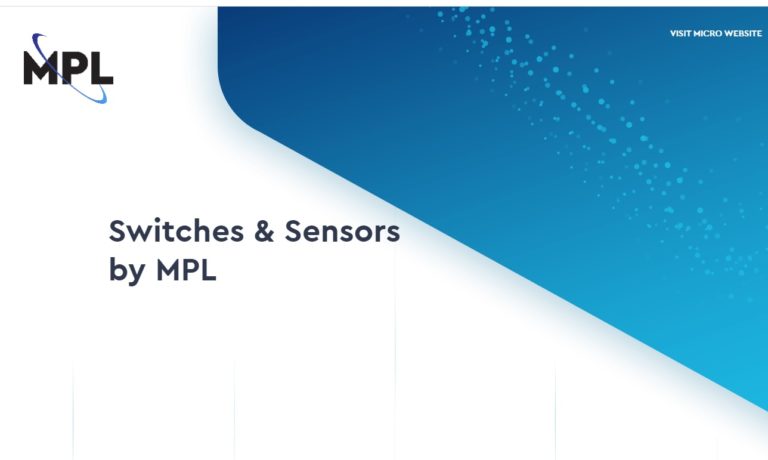
Barksdale Control Products specializes in manufacturing top-quality pressure switches, solid-state pressure switches and other controls which are used for the control and measurement of fluids in industrial applications. Barksdale is a subsidiary of The Crane Company.
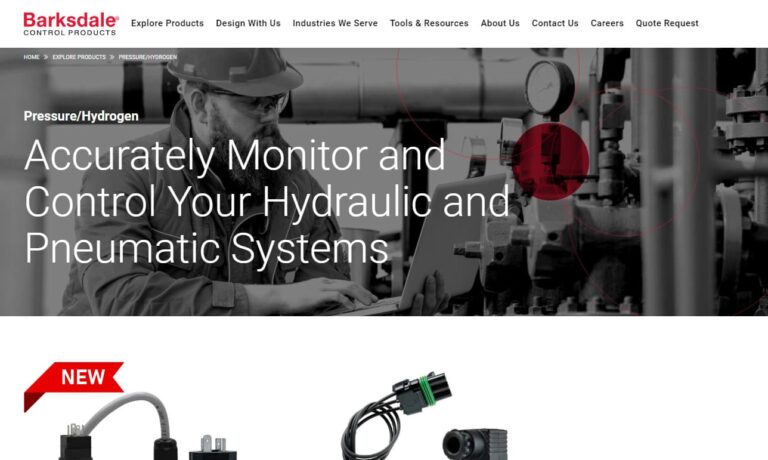
More High Pressure Switch Manufacturers
High-pressure switches monitor the pressure at which the compressor discharges to air and can shut the compressor off if the pressure elevates too high. Low-pressure and high-pressure controls are installed in a single enclosure and function independently via a single switch in dual-pressure controls. Condenser fan cycling and oil pressure safety control are two other uses for mechanical pressure switches.
While seasoned personnel are familiar with mechanical pressure switches and have served the industry well for many years, technological developments are starting to phase them out in favor of electronic controls. This change reflects developments in dozens of other industries where mechanical parts or processes have frequently been replaced by electrical technology.

Design of High-Pressure Switches
High-pressure switches can function at up to 10,000 psig, with an average maximum proof pressure of 4,500 to 7,500 psig. Although pistons, diaphragms, or piezoelectric crystals can operate uncommon, high-pressure switches. The most prevalent high-pressure switches are those with a diaphragm activated by pressure changes. When the flow rate exceeds the set point, the diaphragm is forced open, triggering the actuation and allowing the medium to pass through.
The next widely used high-pressure switch uses a piston that operates much like a valve, opening or shutting in response to high-pressure flow. Last but not least, piezoelectric-actuated high-pressure switches are activated when a voltage is produced by pressing or releasing the piezoelectric crystal. High-pressure switches are primarily differential pressure switches that operate according to a preset point and measure or regulate the difference in pressure between two points. They could, however, also be solid-state or vacuum switches.
Solid-state switches operate electronically and do not need moving parts; instead, they function by opening or closing pressure switch circuits. Vacuum switches control the pressure between two closed cavities by translating a negative pressure signal into an electrical output. Due to the extreme pressure conditions they must withstand, high-pressure switches frequently include different characteristics like explosion-proofing or waterproofing.

Components of High-Pressure Switches
Good pressure switches should have qualities like endurance and tensile strength, with high corrosion resistance preferable though not necessary. They are typically made of aluminum, stainless steel, Monel®, Hastelloy®, and steel.
High-Pressure Switch Applications
These switches are utilized in many different types of equipment, including process equipment, HVAC equipment, pumping systems, compressed air systems, etc.

These switch types are widely utilized in various industrial and manufacturing applications, such as pumps and compressors. In addition, the switches are utilized in manufacturing to regulate equipment, including presses, welding machines, and injection molding machines.
Pneumatic and hydraulic switches control truck air bellows and train brake pressure. These switches can be used in various automobile applications, including power steering, transmissions, and engine oil monitoring. In addition, these switches are used in medical equipment to monitor the pressure of incoming gasses, such as oxygen supply systems.
These switches are employed in filtration systems, blockage detection in various systems, compression units within medical facilities, HVAC boiler room controls, medical breathing apparatus such as ventilators, machineries in agriculture such as crop spraying, water levels in washing machines, and DNA test machines for solution level, among other applications.
How to Calibrate High-Pressure Switches
- The switch must first be connected to the pressure source. For instance, a hand pressure regulator and test gauge connect a pressure source, such as an air supply.
- In the second stage, the switch contacts are continuously checked to see if they are showing as normally closed (NC) or ordinarily opened (NO) using a digital multimeter or an ohmmeter.
- In the third step, the ohmmeter is connected between two switches, such as the NO and NC. Again, ohmmeter readings must be "open circuit." The hand pressure regulator must now be adjusted to increase the pressure toward the switch's setpoint until the switch contacts the switch.
- The ohmmeter should now indicate "short circuit." Don't decrease the pressure reading because this is the switch's set point for increasing pressure.
- The air pressure must then be increased toward the switch to its highest setting in the fourth stage. Once the switch is closed, the pressure is carefully lowered until it is typically open. Again, one should take note of the pressure reading because this is the switch's setting for lowering pressure.
- Check the pressure differential between the rising and decreasing pressure settings in the final step using the values acquired. This pressure check is referred to as the switch's dead band, and the dead band determined must be equal to or lower than the manufacturer's dead band. Typically, the manufacturer will mention the largest dead band value. The switch is unserviceable if the maximum dead band value exceeds the manufacturer's recommendation.
Choosing the Correct High Pressure Switch Supplier
To make sure you have the most constructive outcome when purchasing High Pressure Switches from a High Pressure Switch Supplier, it is important to compare at least 4 to 6 Companies using our list of High Pressure Switch suppliers. Each High Pressure Switch Company has a business profile page that highlights their areas of experience and capabilities and a contact form to directly communicate with the manufacturer for more information or request a quote. Review each High Pressure Switch business website using our proprietary website previewer to get an idea of what each company specializes in, and then use our simple RFQ form to contact multiple High Pressure Switch businesses with the same message.